Sullair Two-Stage Compressors
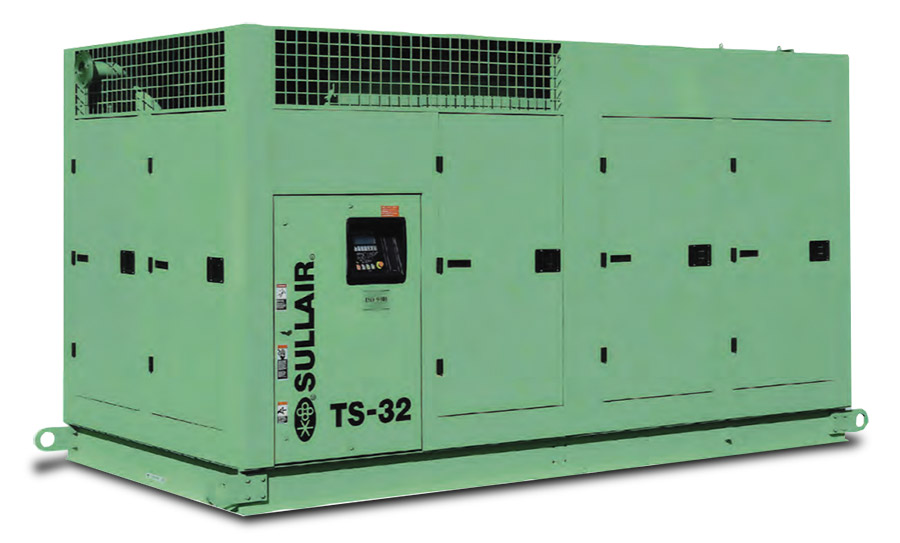
Two-Stage Compression Advantages at Full-Load
Up to 15% power savings
Compared to equally sized single-stage compressors, two-stage compressors offer a 12–15%* power advantage.
- Compression is divided between two stages resulting in power savings
- Reduced differential pressure across each stage minimizes internal leakage losses
Example: A single-stage compressor located at sea level and operating at 100 psig has a 7.9 to 1 compression ratio (in absolute terms).
A two-stage compressor operating at the same altitude and pressure has a 2.1 to 1 compression ratio per stage.
- Unique rotor arrangement engineered for maximum efficiency compared to other two-stage configurations
- Unmatched full-load efficiency—energy savings investment payback in a quickly as two years compared to single-stage compressors
- Match compressed air supply with demand.
- Spiral Valve
- Variable Speed Drive (VSD)
Two-Stage Series tandem compressors use a two-stage rotary screw air end, featuring the Sullair rugged bearing design:
- Tapered roller bearings on the discharge end
- Cylindrical roller bearings on the inlet for high load carrying capacity
Dividing compression across two stages also extends bearing life.
Power: 150–600 hp (112–450 kW)
Delivery: 590–3000 acfm (16.7–84.9 m³/min)
Pressure: 100–175 psi (6.8–12 bar)
Two-Stage Extreme Pressure models available
Power: 200–500 hp (149–373 kW)
Delivery: 500–1350 acfm (14.2–37.8 m³/min)
Pressure: 225–500 psi (15.5–34.5 bar)
Power Savings
per 1000 cfm on TS-32
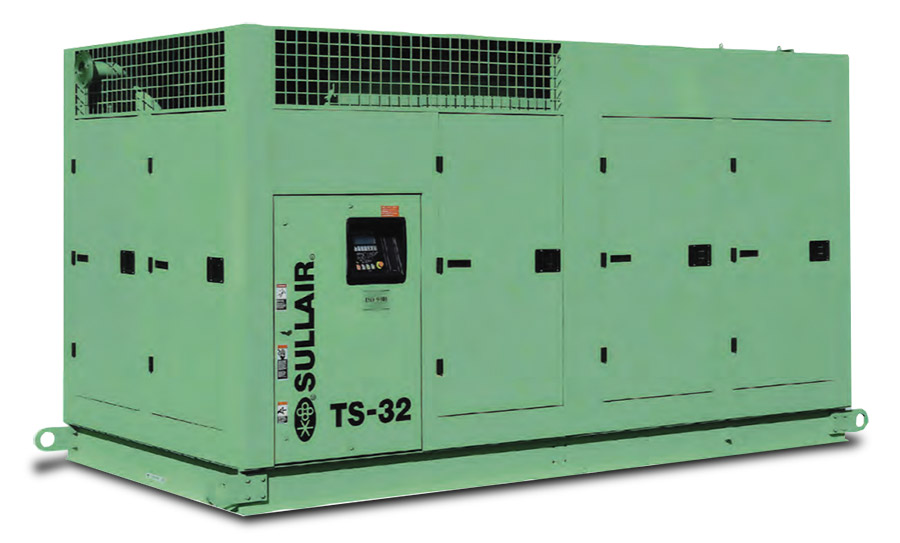
Two-Stage Tandem vs Single-Stage Rotary Screw At Full-Load
At a power cost of $.08/kW/hr, the black dotted line illustrates a tandem two-stage compressor will save $14,373 per 1000 cfm over a typical single-stage compressor operating for 8000 hours at 100 psig.
At a power cost of $.12/kW/hr, the green dotted line shows a $21,560 savings per 1000 cfm over a typical single-stage compressor operating for 8000 hours at 100 psig.
Potential savings may be significantly higher for larger capacity compressors.
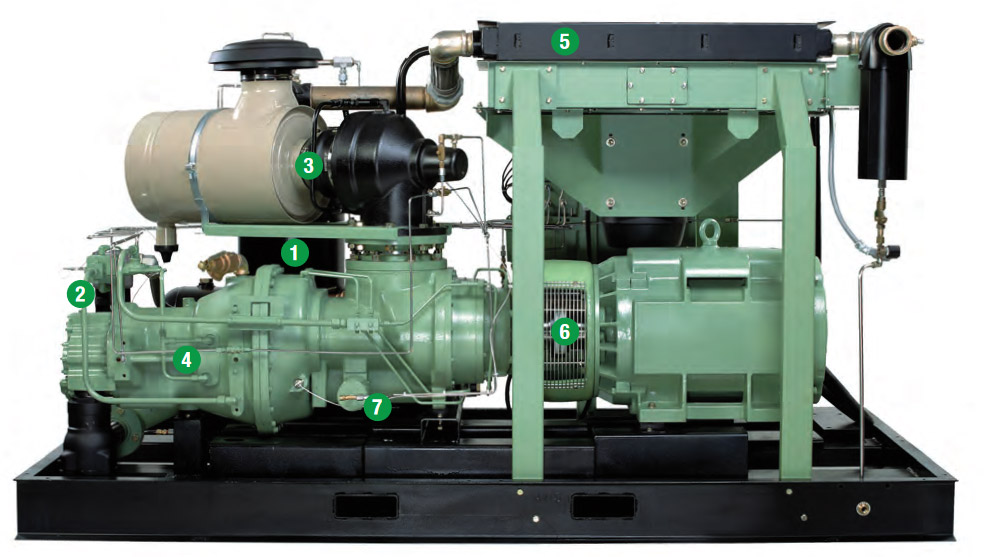
Product Information
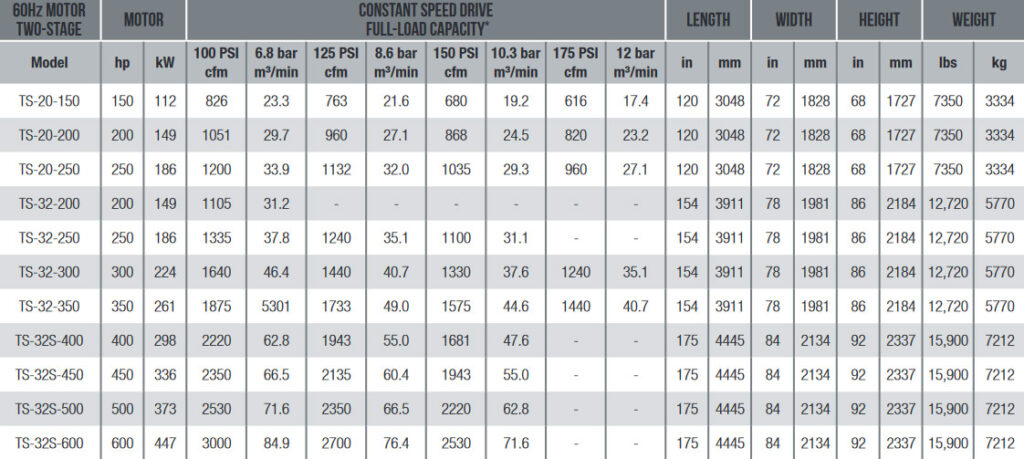
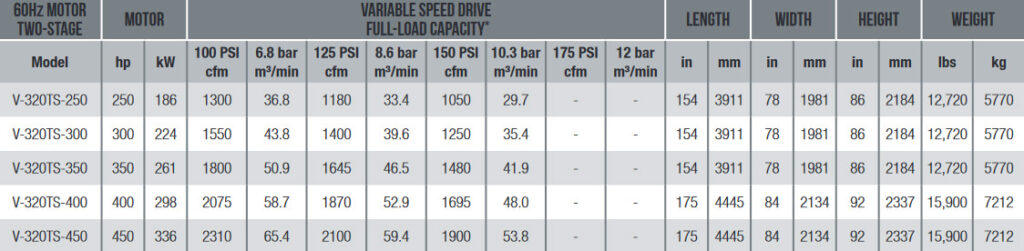
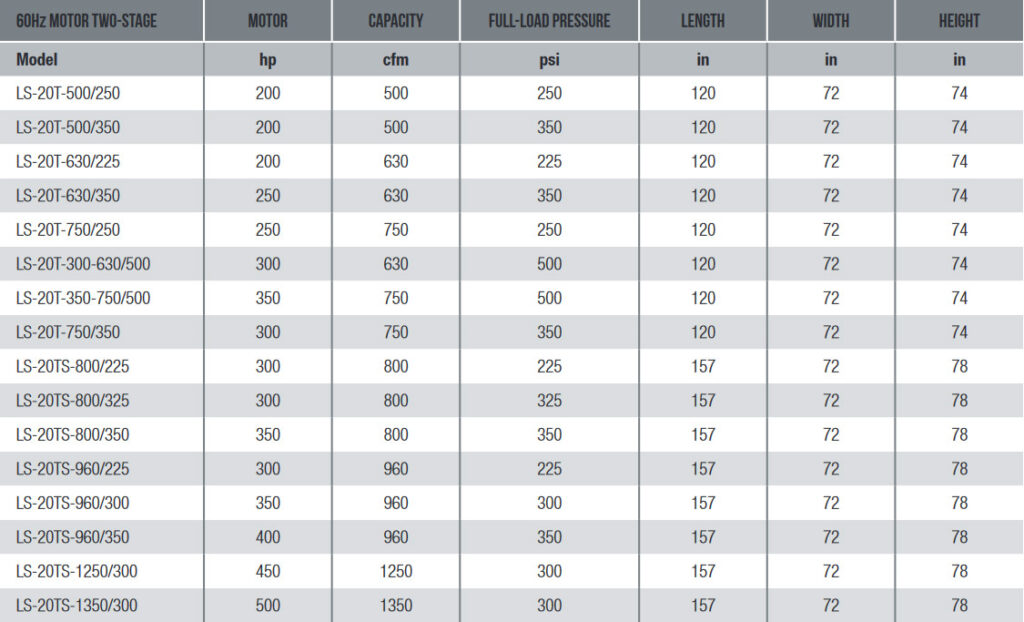